The Comprehensive Guide to China Die Casting Moulds
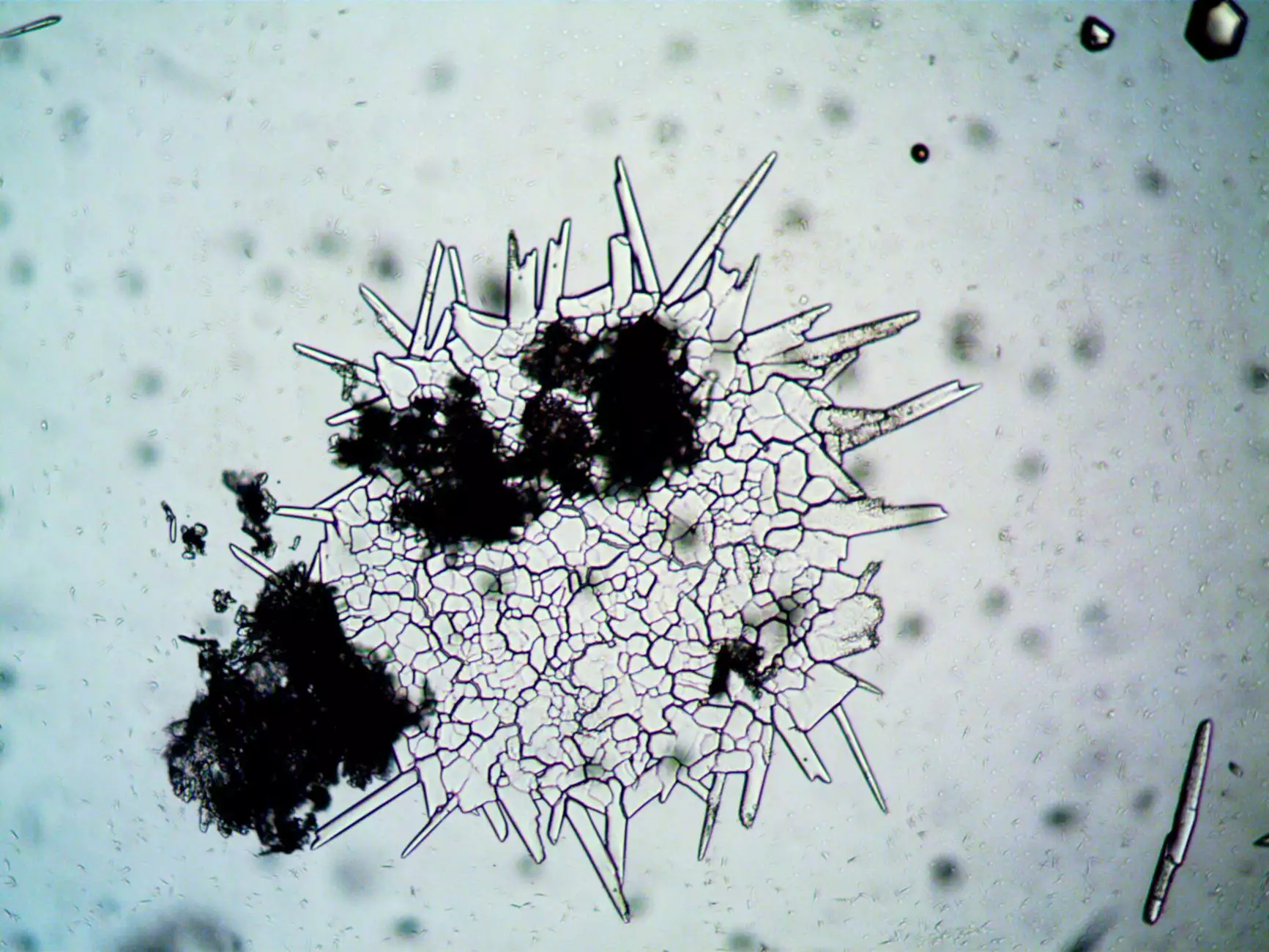
The global manufacturing landscape has continually evolved, and at the forefront of this evolution is the efficiency and precision provided by China die casting moulds. In this extensive article, we will explore the nuances of die casting, its benefits, and why sourcing from China is advantageous for businesses in need of quality metal fabrication.
Understanding Die Casting
Die casting is a metal casting process that involves forcing molten metal under high pressure into a mold cavity. This mold is typically made of hardened steel and can create complex geometries with high precision. The die casting process is instrumental in producing a variety of metallic components used across different industries, including automotive, aerospace, electronics, and consumer goods.
Why Choose China for Die Casting Moulds?
When companies look for die casting solutions, sourcing from China often presents several compelling advantages that are worth considering:
- Cost-Effectiveness: China is renowned for its competitive manufacturing costs. The affordability allows businesses to order high-quality moulds without breaking the bank.
- Advanced Technology: Chinese manufacturers have invested significantly in technology and equipment, which enhances the quality and precision of die casting moulds.
- Skilled Workforce: The workforce in China is skilled and experienced in the art of die casting, ensuring high standards in production.
- Rapid Prototyping: Chinese suppliers are equipped to handle quick prototypes, allowing businesses to test and iterate designs efficiently.
Key Benefits of Using China Die Casting Moulds
Investing in China die casting moulds can yield substantial benefits for businesses seeking to enhance their manufacturing processes:
1. High Precision and Quality
One of the primary advantages of die casting is the remarkable precision it offers. With tiny tolerances, it allows for detailed designs that maintain their integrity, resulting in top-quality finished products. Using Chinese moulds can ensure this precision is met consistently.
2. Diverse Material Options
China's die casting manufacturers provide a range of materials to choose from. Commonly used materials include aluminum, zinc, and magnesium. Depending on the application, businesses can select the most appropriate material for their needs.
3. Enhanced Production Speed
The die casting process is not only efficient but also scalable. Chinese manufacturers uphold robust production methods that can accelerate turnaround times, allowing businesses to meet increasing demand swiftly.
4. Eco-Friendly Manufacturing Practices
As environmental concerns grow, many Chinese manufacturers are adopting eco-friendly practices, using recyclable materials and advancing toward sustainable manufacturing methods, ensuring the production process aligns with global sustainability initiatives.
Critical Considerations When Sourcing Die Casting Moulds
To fully benefit from China die casting moulds, businesses should consider several factors while choosing suppliers:
1. Quality Assurance
Before engaging with any supplier, it’s crucial to assess their quality control measures. Requesting certifications such as ISO 9001 can be helpful in ensuring that the manufacturer follows strict quality standards.
2. Communication
Effective communication is vital to ensure that suppliers understand your specific requirements. Having a proficient team that communicates in English can significantly reduce misunderstandings during the design and production phases.
3. Supplier Reputation
Researching the supplier’s reputation in the industry can save businesses from potential pitfalls. Reading customer testimonials and reviews can provide insights into the company’s reliability and quality of service.
4. Technical Support
Look for suppliers who offer robust technical support throughout the design and production process. This assistance can help resolve any issues quickly and efficiently before they escalate.
The Die Casting Process Explained
To appreciate the value of China die casting moulds, understanding the die casting process is essential:
Step 1: Design the Die
The first step in the die casting process is to design the die, which is a complex form created to manufacture the desired component. The design needs to consider factors such as draft angles, wall thickness, and overall dimensions.
Step 2: Prepare the Mold
A dual-part mold is prepared, usually made from steel or iron, which is meticulously machined. It is essential for the mold to be robust enough to withstand high pressure and maintain its shape over numerous cycles.
Step 3: Melt the Metal
The selected metal is heated to its molten state in a furnace. For aluminum, the melting point is approximately 660°C. The molten metal must be at the right temperature to ensure proper flow into the mold.
Step 4: Inject the Metal
Once the metal is prepared, it is injected into the mold cavity under high pressure using a die casting machine. This process can occur in various cycles, depending on the complexity of the mold design.
Step 5: Cooling and Ejection
After the molten metal fills the cavity, it is allowed to cool and solidify. Once cooled, the mold opens, and the finished part is ejected. It is crucial to precisely manage cooling times for optimal results.
Innovations in Die Casting Technology
The die casting industry is continually evolving, with innovations enhancing the capabilities and efficiencies of manufacturing. Here are some notable advancements:
1. 3D Printing for Mold Design
3D printing technology is becoming increasingly popular for creating complex mold designs quickly and accurately, thus minimizing lead times and costs.
2. Automation and Smart Manufacturing
Many Chinese manufacturers are adopting smart manufacturing practices, employing AI and IoT technology to optimize production processes, quality control, and maintenance scheduling.
3. Enhanced Materials
Development in metal alloys has led to stronger, lighter materials that can withstand higher operating temperatures and environmental stressors, making die-cast products more durable.
Choosing the Right Partner for Die Casting
Selecting an appropriate partner for die casting is crucial for ensuring success in metal fabrication projects. Consider these best practices when evaluating your options:
- Experience: Choose a manufacturer that has a proven track record in the industry, as experience often correlates with quality.
- Portfolio: Review the supplier's past projects to assess their capabilities and ensure they align with your quality and aesthetic standards.
- Customization: Look for suppliers willing to accommodate customization in designs and materials, as flexibility can significantly enhance the business relationship.
- After-Sales Support: Ensure the supplier provides strong after-sales support, including warranty services and product maintenance advice.
Conclusion
In summary, China die casting moulds offer numerous advantages, including cost-effectiveness, high precision, and rapid production capabilities. By understanding the die casting process and the innovations within the industry, businesses can make informed decisions when choosing to source their moulds from China. Selecting the right manufacturing partner can lead to shorter lead times, enhanced product quality, and ultimately, greater success in meeting market demands.
As industries continue to evolve, staying informed about advancements in technology and production techniques will empower businesses to maintain their competitive edge. Investing in quality die casting moulds from reputable Chinese manufacturers can be a game-changer in this regard.