The Importance of Plastic Injection Mold in Metal Fabrication
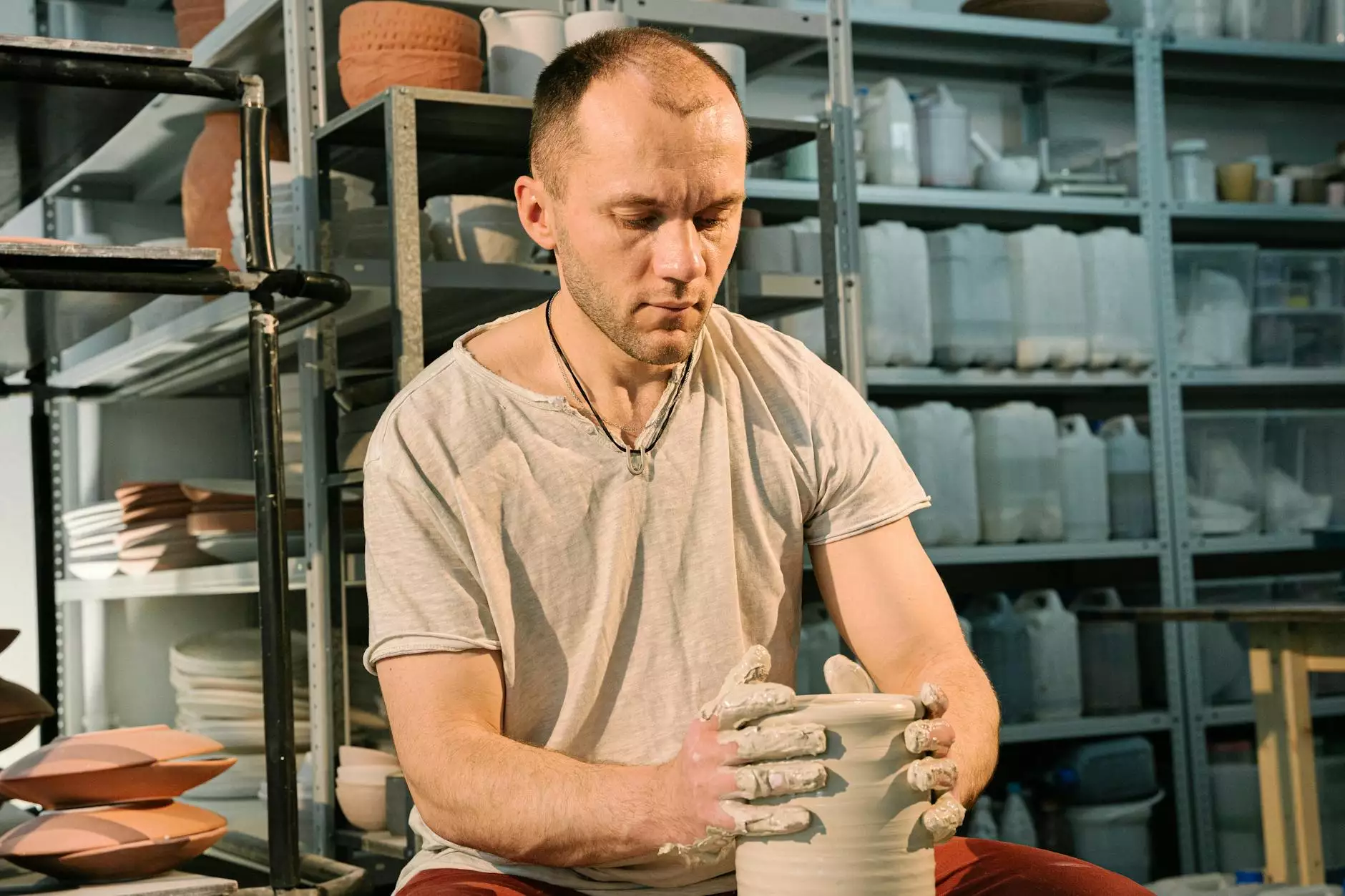
In today's competitive industrial landscape, understanding the role of plastic injection mold in various manufacturing processes is crucial for businesses aiming to enhance efficiency and productivity. As a prominent method in metal fabrication, plastic injection molding has established its importance across different sectors. In this article, we will delve into the intricacies of plastic injection molds, their significant applications, and how they contribute to the evolution of metal fabricators, particularly in the domain of DeepMould.net.
What is Plastic Injection Molding?
Plastic injection molding is a manufacturing process that allows for the efficient production of plastic parts through the injection of molten plastic into a mold. This technique is widely used to create a variety of objects in diverse industries. The plastic injection mold itself is a precision-engineered component designed to cavity specifications, enabling high-volume production with consistency and accuracy.
Key Benefits of Plastic Injection Molding
Embracing plastic injection molding offers several significant advantages:
- High Efficiency: The process allows for rapid manufacturing, making it ideal for high-volume production runs.
- Cost-Effectiveness: Once the initial setup costs are covered, the per-unit cost of molded parts drops considerably.
- Precision Engineering: Modern molds enable the production of highly detailed and complex parts with tight tolerances.
- Material Versatility: A wide range of plastics can be used, including thermoplastics and thermosetting polymers.
- Reduced Waste: The process minimizes material waste compared to traditional subtractive manufacturing methods.
Applications of Plastic Injection Molding in Metal Fabrication
Within the realm of metal fabrication, the use of plastic injection mold is especially critical. Here are some applications where this technology drives innovation:
1. Automotive Industry
In the automotive sector, plastic injection molding is used to manufacture components such as dashboards, door panels, and exterior trim. These parts are crucial for weight reduction and improved fuel efficiency, as modern vehicles increasingly adopt lightweight materials.
2. Consumer Products
Consumer goods, ranging from toys to household appliances, utilize plastic injection molds for their creation. This technology allows for mass production of items that require high detail and reliability.
3. Electronics
In the electronics field, specialized plastic molds are employed to produce enclosures and chassis for devices. The ability to create intricate features and integrate components within one molded part is invaluable.
4. Medical Devices
The healthcare industry leverages plastic injection molding for producing durable and sterile components. This includes everything from syringes to complex instruments that require precision engineering.
Understanding the Plastic Injection Mold Design Process
The design of a plastic injection mold is a crucial element in determining the quality of the finished product. Here are the main phases involved:
1. Concept Development
The initial phase involves understanding the project's requirements and developing ideas that will translate into a workable mold design. Engineers discuss functionality, material selection, and production speed.
2. CAD Modeling
Once the concept is solidified, advanced Computer-Aided Design (CAD) software is used to create a 3D model of the mold. This stage allows for detailed visualization and modifications before production.
3. Mold Fabrication
The mold is then fabricated using high-precision machining processes. This often includes milling, electrical discharge machining (EDM), and grinding to ensure every detail meets specifications.
4. Testing and Prototyping
A prototype is produced and thoroughly tested to ensure it meets quality standards. Adjustments may be made based on feedback to optimize performance.
5. Production and Quality Assurance
Once approved, full-scale production begins. Ongoing quality assurance checks are implemented throughout the manufacturing process to maintain high standards.
Challenges in Plastic Injection Molding
While there are significant benefits to plastic injection molding, some challenges exist that businesses must navigate:
1. Initial Setup Costs
Although the ongoing costs per unit can be low, the initial investment in mold design and fabrication can be substantial.
2. Complexity of Design
Creating multi-part molds with intricate designs can be challenging. It requires skilled engineers and precise manufacturing processes.
3. Material Limitations
Not all materials are suitable for injection molding. Understanding the properties of different plastics is crucial for achieving desired performance.
Future Trends in Plastic Injection Molding
The future of plastic injection molding is promising, especially with these emerging trends:
1. Sustainable Practices
Increasing emphasis on sustainability is driving the development of biodegradable plastics and recycling methods in injection molding.
2. Advanced Technologies
Technological innovations such as 3D printing and smart molds are paving the way for faster prototyping and production processes.
3. Increased Customization
As consumer demand shifts towards more customized products, injection molding processes are evolving to allow for personalization at scale.
Conclusion
In conclusion, the significance of plastic injection mold in metal fabrication cannot be overstated. From automotive parts to medical devices, this versatile manufacturing process underpins a multitude of industries. By understanding its benefits, applications, design processes, and future trends, businesses can harness the power of plastic injection molding to innovate and stay competitive in the market. At DeepMould.net, we are committed to providing advanced solutions in plastic injection molding, enabling businesses to thrive in an ever-evolving landscape.
For more information on how plastic injection molding can benefit your business, visit our website or contact us today!